Pill Cutter - Progress Blog 3: 10/16/2021
- Daniel Cedillo
- Oct 16, 2021
- 4 min read
Hello and welcome back to our team's third blog post! This is a blog for the University of Houston's Mechanical Engineering Capstone Team 35: Progress Blog 3.
Firstly, we would like to talk about the work the team has completed up to now. Thus far, the team has resolved several issues with the constraints of the design. The team has researched several current pill cutters to determine the dimensions and weight the device should be around; it has been determined that the device’s dimensions should be around 4x6x3 inches and have a maximum volume of 72 cubic inches and the weight should be a maximum of 0.75 pounds. Also, the team has found out the maximum force that needs to be applied on the device to split the pills.
Other than updating the constraints, the team has determined an effective validation plan, a deliverable list, and a Gantt chart, shown below in figure 1, to plan out the work that needs to be done for the rest of the semester. The deliverables list includes schematics of design components and assembly, a completed physical working prototype and an instruction manual.
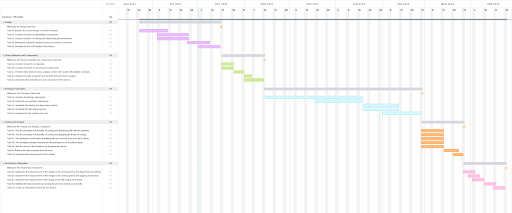
Figure 1: Gantt Chart.
Also, the team has developed a CAD model of one of the components of the device. The team has decided to implement a disk structure for the device that has different areas to place the pill depending on the shape; a proposed design for the structure is shown below in figure 2.

Figure 2: Multiple-shaped disk.
Additionally, the team has created a rough CAD model of the storage mechanism, as shown below on Figure 3. The mechanism consist of trap doors located where the pills will be cut and the user will open these doors to let the cut pill fall into its respective storage.

Figure 3: Pill storage mechanism.
Next, we would like to explain some of the challenges that the team has been faced with.
The first challenge is the development of the holding mechanism to hold the pill in place. Based on research the team has done, the pill cannot be fully constrained in order to avoid crushing the pill during the cutting process. However, the pill should be held in place in order to make sure the pill is placed correctly on the cutting area so that the pill can be split evenly. Currently, the team is trying to develop a mechanism that would hold the pill in the area by using shaped walls that push against the pill on each side by using springs.
The second challenge is determining the dimension of each component. Since the cutting mechanism will work as a class II lever, the team wants to maximize the mechanical advantage of the device by increasing the distance from the fulcrum of the lever to the applied force and decreasing the distance from where the pill will be cut to the fulcrum. The team is having a difficult time in figuring out how to scale each component of the device.
The third challenge is in acquiring the information necessary to justify some of the design components. For example, the team’s instructor advised us that we need to research the force necessary for current solutions in order to see whether our device could make an improvement in this aspect. The team has had a difficult time figuring this out since research on existing pill cutters is limited.
Moving forward, concerning the team’s projected work plan for the next two weeks, we will first need to finish the necessary CAD models of the overall device, as well as work on presentations for it. These CAD models will include the holding/disc portion, the cutting mechanism, and the storing container. All dimensions of the CAD should of course be accurate to the tolerances we have found.
Furthermore, we will conduct research on materials and internal components we believe to be best suited to the device. The materials will factor into the device’s durability, cost, and ease of manufacturing. So too will the mechanical components, on top of functionality.
Once we have established the materials which will be used, along with the components, we may begin the finite stress analysis on the CAD. This will be done using computer software to obtain the most accurate results a simulation can provide. It is our objective that principal loads are taken into account during the simulation, so that the team can verify that the device will work as intended.
With this, we may elaborate on anticipated challenges for the team’s projected work plan. First, the team will need to finalize all design considerations thus far for the CAD. While the team has narrowed down many designs already, going forward, the team will need to stick to one model. After this, as the second challenge, the team will have to consider a schematic for the device. This will entail an internal layout for all components, as well as identifying what materials will be used where. The team will not be able to run an accurate computer simulation without this information and insight.
Comments